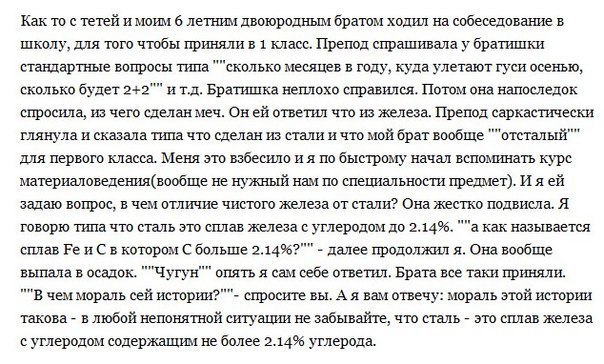
храч
2013-10-25 22:07:58 #
прямо второй квейк какой-то. впрочем, четыре китайца сделали бы это быстрее и дешевле.
2013-10-25 22:11:14
кто-нибуть выло жите уже график зависимости быстроты и дишевизны от количества китайцев бесплатно онлайн спасибопожалуйста
2013-10-25 22:12:45
а меня когда так собеседовали в голову, я еле собеседовывание прошел, потому что стеснялся отвечать на тупые вопросы с очевидными ответами. было неловко за вопрошающига. мол, я отвечу и он покраснеет от стыда; зачем же ставить его в неловкое положение. тьфу.
2013-10-25 22:24:29
вниманию свалконаучьной апчествинасте прецтавляю график зависимости дешевизны от четырех кетайцов.
отрисовал качиствина как смок. извените.
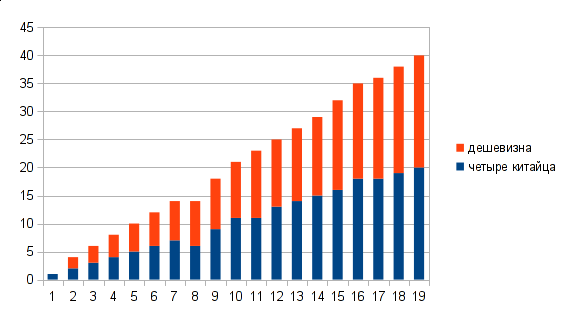
отрисовал качиствина как смок. извените.
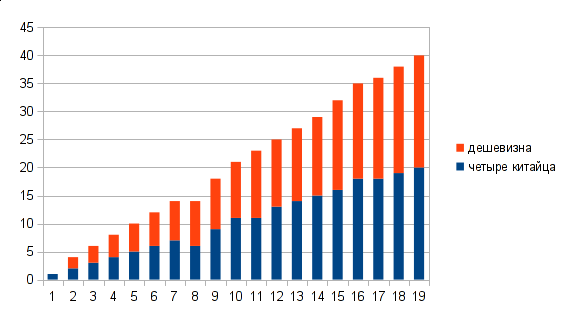
2013-10-25 22:36:31
а миня, помню, када таг со, прастите, биседовали, интересовались исчо, могу ли я посчитать до ста.
Но ста это же очень много, можно сказать просто дофига. И считать до него очень долго.
Поэтому я был вынужден честна ответить, что могу но только с отсановками, потому что при таком долгом деле надо отдыхать иногда.
Вот.
А какая здесь мораль я не знаю, уж прастити-извинити. И так слишком много букав нопесал.
Но ста это же очень много, можно сказать просто дофига. И считать до него очень долго.
Поэтому я был вынужден честна ответить, что могу но только с отсановками, потому что при таком долгом деле надо отдыхать иногда.
Вот.
А какая здесь мораль я не знаю, уж прастити-извинити. И так слишком много букав нопесал.
2013-10-25 23:01:11
а вот што тежелее - килограм стали и килаграм железа? думаю, первый класс - не про васс
2013-10-25 23:07:35
вапщето у кетайцеф долженбыть пластмасавый мечь
ну или цемент
или на худой конец 2 працента углерода
ну или цемент
или на худой конец 2 працента углерода
2013-10-26 00:04:04
увгн Заебурии, это что жи палучаитсо, нужно каминь посыпать перцем? ? я чтото нипони
2013-10-26 00:41:27
Поскольку железо является основной составной частью металлической шихты и готовой стали, его баланс в процессе плавки влияет на очень важные технико-экономические показатели сталеплавильного производства — расход металлической шихты и выход годного металла. Под расходом металлической шихты (ηмш, кг) обычно понимают расход чугуна (Gчуг, т) и лома (Gл, т), отнесенный к 1 т готовой (годной) стали-слитков или литых заготовок (Gг.с, т):
Баланс железа при плавке стали (часть 1)
Поскольку в процессе плавки и разливки неизбежны угар железа и его примесей и другие потери, то Gг.с1000. Средний расход металлической шихты обычно составляет 1100—1130 кг/т.
За выход годного (gг.с, %) принимают отношение количества полученной годной стали к массе всех израсходованных металлических материалов — чугуна, лома, ферросплавов (GFеE) и железа твердых окислителей Gm.oFе:
Баланс железа при плавке стали (часть 1)
Обычно gг.с=88—92%, и его повышение является важной задачей при плавке стали. Одним из способов уменьшения расхода металлической шихты и повышения выхода годного является уменьшение потерь железа во время плавки. Эти потери обычно определяют составлением баланса железа. Наиболее распространенным и удобным методом является составление баланса для 100 кг металлической шихты (чугуна и лома). Ниже все материальные балансы (частные и общие) составлены по этому методу. Если рассматривать плавку в целом, не включая разливку, то баланс железа состоит из следующих основных статей:
Баланс железа при плавке стали (часть 1)
Деление баланса на приходную и расходную часть относительно железа твердых окислителей и оксидов железа шлака является условным и принято для упрощения расчетов. В действительности часть железа твердых окислителей остается в шлаке в виде невосстановленных оксидов, а часть железа металлической фазы, окисляясь, переходит в шлак. Рассмотрим возможные изменения отдельных статей баланса железа.
Железо металлической шихты (чугуна и лома) зависит от содержания примесей в чугуне и ломе и их соотношения в шихте (расхода). Приняв суммарный расход чугуна и лома за 100%, рассматриваемую зависимость можно представить графически (рис. 23).
Баланс железа при плавке стали (часть 1)
Как видно из рис. 23, влияние расхода и состава чугуна на количество железа в шихте существенно. Так, среднее значение gм.Fe в дуговом электрическом процессе составляет 97,5%, тогда как в кислородно-конвертерном процессе ~94,5%. Это различие в количестве железа в шихте (~3%) влияет на расход металлической шихты и на выход готовой стали: при прочих равных условиях чем больше расход чугуна в шихту, тем больше расход металлической шихты и меньше выход годного металла. Следовательно, неодинаковые расход металлической шихты и выход годного, наблюдаемые в разных сталеплавильных процессах, в значительной степени объясняются различной долей чугуна в шихте.
При высоком расходе чугуна, например в кислородно-конвертерном процессе, колебания содержания примесей в чугуне также могут вызвать существенное изменение (до 2%) количества железа в шихте и расхода металлической шихты (выход годного).
Для одного и того же завода общее содержание примесей в чугуне и ломе, их соотношение в шихте обычно изменяются в узких пределах, поэтому количество железа в шихте изменяется незначительно и его влияние на расход металлической шихты и выход годного несущественно. Но на разных заводах может наблюдаться не только большое различие в расходе чугуна, связанное с различием процесса и типа агрегата, но и в содержании примесей в металлической шихте. С этим связано значительное различие содержания железа в металлической шихте, расхода металлической шихты и выхода годного (4—5%, см. рис. 23), что необходимо учитывать при сопоставлении и оценке технико-экономических показателей работы различных заводов.
Железо твердых окислителей (железной руды, агломерата, окатышей и т. п.) зависит от их расхода на плавку и содержания железа в твердом окислителе. В любом сталеплавильном процессе, кроме конвертерного на воздушном дутье, расходуют то или иное количество твердого окислителя. Минимальный расход его (0,5—1%) наблюдается во всех современных кислородных процессах, проводимых в конвертерах, мартеновских и двухванных печах. При таком расходе количество железа твердых окислителей колеблется в пределах 0,3—0,5%. Максимальный расход (15—20%) твердых окислителей при мартеновском скрап-рудном процессе, осуществляемом с высоким расходом чугуна, без продувки ванны кислородом. В этом случае количество железа твердых окислителей обычно колеблется в пределах 8—12%. Это колебание зависит от расхода чугуна и окислительного потенциала газовой фазы печи. Таким образом, расход твердых окислителей, зависящий от типа процесса, существенно влияет на баланс железа и, следовательно, на расход металлической шихты (выход годного); это влияние значительно больше влияния изменения расхода чугуна и его состава.
Железо флюсов в общем случае может изменяться от пренебрежимо малых значений до нескольких процентов в зависимости от вида применяемых флюсов.
Если основным флюсом является обычная известь, а дополнительным — плавиковый шпат, то поступление железа в ванну пренебрежимо мало, поскольку указанные материалы оксидов железа содержат в небольших количествах.
Когда в качестве дополнительного флюса используется боксит, в котором содержание железа обычно изменяется в пределах 20—30% и расход которого составляет 1—2%, эта статья может составлять 0,2—0,3%.
Если же в качестве флюса используется ожелезненная известь, полученная по современной технологии (из смеси порошков извести и твердого окислителя), то железо флюсов может доходить до 1,0—1,5% и более.
Железо ферросплавов (раскислителей и легирующих) также зависит от их расхода, содержания в них железа. Обычно в ферросплавах содержание железа колеблется в пределах 25—55%. Расход ферросплавов зависит от состава выплавляемой стали. Минимальный расход (0,5—1,5%) имеет место при выплавке углеродистых сталей. При выплавке низко- и среднелегированных сталей расход ферросплавов обычно составляет 3—10%. Следовательно, количество железа ферросплавов обычно при выплавке углеродистых сталей составляет 0,2—0,8%, при выплавке легированных сталей 1—5%.
Железо готовой стали зависит от ее выхода и содержания в ней примесей. Выход жидкого металла в подовом процессе без продувки ванны кислородом обычно составляет 98—103%, в кислородных процессах 88—92%. Содержание примесей в готовом металле зависит от его состава: в углеродистых сталях 1—2%, в легированных 3—10% и более, поэтому количество железа готовой стали обычно составляет: при выплавке углеродистых сталей в подовых агрегатах 96—102% и кислородных агрегатах 86—91%, при выплавке легированных сталей — соответственно 90—100 и 80—90% и менее.
Железо шлака в виде оксидов зависит от количества шлака и содержания в нем железа в виде оксидов. Обычно в процессах плавки стали в подовых агрегатах и кислородных конвертерах образуется шлака 10—20% от массы металла, и среднее содержание оксидов железа в шлаке составляет 10—15%, поэтому потеря железа на образование шлака в среднем составляет 0,8—2%, но в отдельных случаях (при большом выходе шлака и высоком содержании оксидов железа в нем) может достигать ≥3%. Значительно больший выход шлака обычно имеет место при переделе высокофосфористых чугунов, и избежать этого невозможно. Выход шлака также зависит от количества чугуна в шихте и содержания в нем кремния: чем больше расход чугуна и содержание в нем кремния, тем больше выход шлака, если другие условия остаются постоянными.
Высокое содержание оксидов железа в шлаке при нормальном нагреве ванны наблюдается при малых концентрациях углерода в металле (см. рис. 22), когда оно снижается до <0,1% и особенно до <0,05%. Например, при <0,05% С количество оксидов железа в шлаке повышается до 30—40%. Такие низкие концентрации углерода и соответствующие им высокие содержания оксидов железа в шлаке могут быть только в конце плавки при выплавке низкоуглеродистой стали. Для снижения потери железа в шлаке в виде оксидов при выплавке стали с таким низким содержанием углерода необходимо по достижении в металле 0,10—0,15% С возможно полнее скачивать шлак из агрегата и заканчивать плавку с небольшим количеством конечного шлака.
"В чём мораль этой истории?", - спросите Вы. А я вам отвечу: мораль этой истории такова - в любой непонятной ситуаии не забывайте, что есть ситуации ещё непонятнее, чем эта.
Баланс железа при плавке стали (часть 1)
Поскольку в процессе плавки и разливки неизбежны угар железа и его примесей и другие потери, то Gг.с1000. Средний расход металлической шихты обычно составляет 1100—1130 кг/т.
За выход годного (gг.с, %) принимают отношение количества полученной годной стали к массе всех израсходованных металлических материалов — чугуна, лома, ферросплавов (GFеE) и железа твердых окислителей Gm.oFе:
Баланс железа при плавке стали (часть 1)
Обычно gг.с=88—92%, и его повышение является важной задачей при плавке стали. Одним из способов уменьшения расхода металлической шихты и повышения выхода годного является уменьшение потерь железа во время плавки. Эти потери обычно определяют составлением баланса железа. Наиболее распространенным и удобным методом является составление баланса для 100 кг металлической шихты (чугуна и лома). Ниже все материальные балансы (частные и общие) составлены по этому методу. Если рассматривать плавку в целом, не включая разливку, то баланс железа состоит из следующих основных статей:
Баланс железа при плавке стали (часть 1)
Деление баланса на приходную и расходную часть относительно железа твердых окислителей и оксидов железа шлака является условным и принято для упрощения расчетов. В действительности часть железа твердых окислителей остается в шлаке в виде невосстановленных оксидов, а часть железа металлической фазы, окисляясь, переходит в шлак. Рассмотрим возможные изменения отдельных статей баланса железа.
Железо металлической шихты (чугуна и лома) зависит от содержания примесей в чугуне и ломе и их соотношения в шихте (расхода). Приняв суммарный расход чугуна и лома за 100%, рассматриваемую зависимость можно представить графически (рис. 23).
Баланс железа при плавке стали (часть 1)
Как видно из рис. 23, влияние расхода и состава чугуна на количество железа в шихте существенно. Так, среднее значение gм.Fe в дуговом электрическом процессе составляет 97,5%, тогда как в кислородно-конвертерном процессе ~94,5%. Это различие в количестве железа в шихте (~3%) влияет на расход металлической шихты и на выход готовой стали: при прочих равных условиях чем больше расход чугуна в шихту, тем больше расход металлической шихты и меньше выход годного металла. Следовательно, неодинаковые расход металлической шихты и выход годного, наблюдаемые в разных сталеплавильных процессах, в значительной степени объясняются различной долей чугуна в шихте.
При высоком расходе чугуна, например в кислородно-конвертерном процессе, колебания содержания примесей в чугуне также могут вызвать существенное изменение (до 2%) количества железа в шихте и расхода металлической шихты (выход годного).
Для одного и того же завода общее содержание примесей в чугуне и ломе, их соотношение в шихте обычно изменяются в узких пределах, поэтому количество железа в шихте изменяется незначительно и его влияние на расход металлической шихты и выход годного несущественно. Но на разных заводах может наблюдаться не только большое различие в расходе чугуна, связанное с различием процесса и типа агрегата, но и в содержании примесей в металлической шихте. С этим связано значительное различие содержания железа в металлической шихте, расхода металлической шихты и выхода годного (4—5%, см. рис. 23), что необходимо учитывать при сопоставлении и оценке технико-экономических показателей работы различных заводов.
Железо твердых окислителей (железной руды, агломерата, окатышей и т. п.) зависит от их расхода на плавку и содержания железа в твердом окислителе. В любом сталеплавильном процессе, кроме конвертерного на воздушном дутье, расходуют то или иное количество твердого окислителя. Минимальный расход его (0,5—1%) наблюдается во всех современных кислородных процессах, проводимых в конвертерах, мартеновских и двухванных печах. При таком расходе количество железа твердых окислителей колеблется в пределах 0,3—0,5%. Максимальный расход (15—20%) твердых окислителей при мартеновском скрап-рудном процессе, осуществляемом с высоким расходом чугуна, без продувки ванны кислородом. В этом случае количество железа твердых окислителей обычно колеблется в пределах 8—12%. Это колебание зависит от расхода чугуна и окислительного потенциала газовой фазы печи. Таким образом, расход твердых окислителей, зависящий от типа процесса, существенно влияет на баланс железа и, следовательно, на расход металлической шихты (выход годного); это влияние значительно больше влияния изменения расхода чугуна и его состава.
Железо флюсов в общем случае может изменяться от пренебрежимо малых значений до нескольких процентов в зависимости от вида применяемых флюсов.
Если основным флюсом является обычная известь, а дополнительным — плавиковый шпат, то поступление железа в ванну пренебрежимо мало, поскольку указанные материалы оксидов железа содержат в небольших количествах.
Когда в качестве дополнительного флюса используется боксит, в котором содержание железа обычно изменяется в пределах 20—30% и расход которого составляет 1—2%, эта статья может составлять 0,2—0,3%.
Если же в качестве флюса используется ожелезненная известь, полученная по современной технологии (из смеси порошков извести и твердого окислителя), то железо флюсов может доходить до 1,0—1,5% и более.
Железо ферросплавов (раскислителей и легирующих) также зависит от их расхода, содержания в них железа. Обычно в ферросплавах содержание железа колеблется в пределах 25—55%. Расход ферросплавов зависит от состава выплавляемой стали. Минимальный расход (0,5—1,5%) имеет место при выплавке углеродистых сталей. При выплавке низко- и среднелегированных сталей расход ферросплавов обычно составляет 3—10%. Следовательно, количество железа ферросплавов обычно при выплавке углеродистых сталей составляет 0,2—0,8%, при выплавке легированных сталей 1—5%.
Железо готовой стали зависит от ее выхода и содержания в ней примесей. Выход жидкого металла в подовом процессе без продувки ванны кислородом обычно составляет 98—103%, в кислородных процессах 88—92%. Содержание примесей в готовом металле зависит от его состава: в углеродистых сталях 1—2%, в легированных 3—10% и более, поэтому количество железа готовой стали обычно составляет: при выплавке углеродистых сталей в подовых агрегатах 96—102% и кислородных агрегатах 86—91%, при выплавке легированных сталей — соответственно 90—100 и 80—90% и менее.
Железо шлака в виде оксидов зависит от количества шлака и содержания в нем железа в виде оксидов. Обычно в процессах плавки стали в подовых агрегатах и кислородных конвертерах образуется шлака 10—20% от массы металла, и среднее содержание оксидов железа в шлаке составляет 10—15%, поэтому потеря железа на образование шлака в среднем составляет 0,8—2%, но в отдельных случаях (при большом выходе шлака и высоком содержании оксидов железа в нем) может достигать ≥3%. Значительно больший выход шлака обычно имеет место при переделе высокофосфористых чугунов, и избежать этого невозможно. Выход шлака также зависит от количества чугуна в шихте и содержания в нем кремния: чем больше расход чугуна и содержание в нем кремния, тем больше выход шлака, если другие условия остаются постоянными.
Высокое содержание оксидов железа в шлаке при нормальном нагреве ванны наблюдается при малых концентрациях углерода в металле (см. рис. 22), когда оно снижается до <0,1% и особенно до <0,05%. Например, при <0,05% С количество оксидов железа в шлаке повышается до 30—40%. Такие низкие концентрации углерода и соответствующие им высокие содержания оксидов железа в шлаке могут быть только в конце плавки при выплавке низкоуглеродистой стали. Для снижения потери железа в шлаке в виде оксидов при выплавке стали с таким низким содержанием углерода необходимо по достижении в металле 0,10—0,15% С возможно полнее скачивать шлак из агрегата и заканчивать плавку с небольшим количеством конечного шлака.
"В чём мораль этой истории?", - спросите Вы. А я вам отвечу: мораль этой истории такова - в любой непонятной ситуаии не забывайте, что есть ситуации ещё непонятнее, чем эта.
2013-10-26 01:10:48
>каминь всиму галова!
Хорошо, когда каминь - голова, но плохо, когда голова - каминь.
Ну, или наобород.
Хорошо, когда каминь - голова, но плохо, когда голова - каминь.
Ну, или наобород.
2013-10-26 03:31:10
мне в розскази увга ипшайтега очинь понравелось то што митал годнэ и што лом. пажалусто передайти привет маме и скожыте што гогда я джве недели на зад вшутку прыгнул в уходящэ поест он ехол в хобароск и я низнаю как отсюдо поэвонить.
2013-10-26 12:18:00
а потом этот мальчик вырос и стал несмешно комментить на свалке. возможно, это даже ХЗ кто
2013-10-26 16:51:22
Двоюродный брат во время драки вспомнил, чему его учил отец, но то что сталь - сплав железа с углеродом содержащим не более 2.14% углерода ему никак не пригодилось.
2013-10-28 08:22:45
сщетаю псто с очевиднэм преимущиствам показывае, што сцайт про свалго стал (пре в рот илсо) образаватильнэ сцайтом, и умнэ очинь. што вы не вериле, а я ещё тагда абэтам ствел на вид.
2018-06-17 20:15:38
Ну уж если на то пошло, то в сталях бываюд легирующие добавки, многие тыщи лет мечи делали в основном из бронзы, а ищо на мечах рукояти всякой шнягой обматывались и укрощались джрагоцэнными камниями.
А учителнитце можно зозодать вопроэ, из чего сделано железо.
Варианты нопремер:
1) из протонов, нейтронов, электронов и сил между ними.
2) из железной руды.
какой бы вариант не ответила - ткнуть её обучалом в другой правельный атвет
А учителнитце можно зозодать вопроэ, из чего сделано железо.
Варианты нопремер:
1) из протонов, нейтронов, электронов и сил между ними.
2) из железной руды.
какой бы вариант не ответила - ткнуть её обучалом в другой правельный атвет
2018-06-17 20:38:38
нам нидавно на уроке росказывале чшто в джревнем риме чугунарии злоупотребляле лигирующеми добавкаме и от этово палучались лигионеры